Advanced Inventory Management
Build an advanced inventory management playbook to get your customers what they need, when they need it.
Speak With A Representative
Request Content Access
Our systems detected an issue with your IP. If you think this is an error please submit your concerns via our contact form.
Businesses need to transform the way they think about inventory in this evolving environment. The COVID-19 pandemic added to challenges created by geopolitical events, resulting in significant disruptions to global supply chains. Businesses were hit by the perfect storm: material shortages, sick and absent workers, logistical delays, and rising prices. Add to that rising competition, demand fluctuations, and the complexities from omnichannel fulfillment, and it is clear this is the right time to revisit established inventory management practices and policies.
Our Advice
Critical Insight
Two attributes of supply chains have become increasingly important in today’s challenging operating environment: supply chain agility and resiliency. Agility refers to the ability to rapidly respond to short-term operational issues as they appear. Resiliency refers to restructuring supply chains using supporting technology to withstand future challenges of the scale seen during the pandemic. This research explains how effective, technology-led inventory management can help achieve both agility and resiliency.
Impact and Result
Effective, technology-led inventory management can help address supply chain challenges. This research presents a playbook to deploy advanced technology and improve your inventory management maturity. Critical components of this playbook include an overview of inventory management systems and their advanced capabilities, an introduction to KPIs for effective performance management, and a technology maturity map to show you what good inventory management looks like. This will ultimately arm you with the ability to plan better, procure more efficiently, and fulfill in an optimized manner across more channels, customer types, and geographies.
Advanced Inventory Management Research & Tools
1. Advanced Inventory Management Storyboard – Research that discusses the genesis of modern supply chain problems, outlines the components of an inventory management playbook, and unpacks features of modern inventory management systems.
The purpose of this research is to introduce the inventory management playbook, a technology maturity framework, and an overview of advanced inventory management features.
2. Inventory Management Maturity Self-Assessment – A template to help understand the current state of inventory management in your organization with a defined set of steps to reach the next maturity level.
A worksheet to analyze the current state of inventory management and understand attributes of other maturity levels.
Speak With A Representative
Request Content Access
Our systems detected an issue with your IP. If you think this is an error please submit your concerns via our contact form.
Advanced Inventory Management
Get your customers what they need, when they need it.
Analyst Perspective
Get your customers what they need, when they need it.
In 2015, Microsoft cofounder Bill Gates dramatically rolled a barrel of survival supplies from the Office of Civil Defense onto the stage for a TED Talk titled “The next outbreak? We’re not ready.” Gates predicted, based on the global response to the Ebola epidemic in 2014, that another viral outbreak would wreak havoc because of how unprepared we were. When COVID-19 began to spread worldwide, we did not have enough epidemiologists or medical workers, and we had no idea of treatment approaches. To prevent this from happening again, we need to use technology to build a playbook to respond effectively. This holds true for modern supply chains, as well.
From identifying new suppliers and switching modes from sea to air to managing promotional pricing followed by price hikes due to variability in demand and supply, businesses had to deal with multiple risk management scenarios during the COVID-19 pandemic. The backbone on which global supply chains had been built, just-in-time inventory management, was shattered by the pandemic and other geopolitical events.
Is the answer, then, to be more agile or resilient, or both? Agility is great for responsiveness, whereas resilience involves preparing for an eventual shock to the system. Agility is difficult to achieve when all your supply comes from one country or supplier and you maintain low or almost no safety/buffer stock, depend on one mode of transportation, and rely heavily on physical stores to sell your inventory. In comparison, resilience requires significant physical changes to supply chains. McKinsey & Company says “it’s quicker to build inventories than factories,” and that is what most businesses have done as a temporary solution to challenges from the pandemic. For the long term, businesses will have to balance regionalization as a means of risk aversion with digitalization as a means of capability building. This is where an inventory management playbook can help. In this research, we help you unpack and analyze the components of an inventory management playbook and study advanced features of inventory management systems that can be deployed to get you ready for the next shock to your supply chain.
Shreyas Shukla
Principal Research Director, Manufacturing Industry
Info-Tech Research Group
Executive Summary
Your ChallengeBusinesses have endured shocks to the supply chain from the COVID-19 pandemic. Supply chain issues have significant impacts, such as:
Global trade wars, the Russia-Ukraine war, and inflation have put additional pressures on supply chains, adding to cost and procurement challenges. |
Common ObstaclesNew suppliers need to be located. Most businesses are struggling with the chaos of having to locate alternative suppliers, as well as experiencing fulfillment delays, rising prices, material shortages, and lack of staff. This is the right time to revisit your inventory management policies. Omnichannel and e-commerce are here to stay. In addition, businesses are having to create unique partnership models in collaboration with their suppliers and retailers to provide their customers with an enhanced shopping experience. Supply issues, rising prices, logistics, and labor issues are here to stay, at least in the immediate term. Businesses will need to transform the way that they think about inventory in this evolving environment. |
Info-Tech’s ApproachBusinesses have realized that they will have to be agile in the short term by responding to challenges that appear, as well as resilient in the long term by restructuring their supply chain using supporting technology, to withstand future challenges of the scale seen during the COVID-19 pandemic. We intend to support this direction by providing:
|
Info-Tech Insight
The most critical aspect of any inventory management playbook will be the inventory management system, which will ultimately help businesses plan better, procure more efficiently, and fulfill in an optimized manner across more channels, customer types, and geographies.
Overview of the inventory management ecosystem
Inventory management is the monitoring and supervision of the flow of materials, resulting in finished goods. Inventory management covers processes such as procurement, production, storage, distribution, and sales. It is enabled by full transparency of your supply chain and the required inventory levels of raw materials, work in progress, and finished goods. Good inventory management enables your business by ensuring that finished goods are available for customers to buy and that enough raw materials are at hand to continue production and meet demand.
Source: SelectHub, 2019
Inventory management challenges originate from internal and external factors
Common operational problems that companies face due to poor planning, manual processes, and impractical policies, as well as headwinds and disruptions from external factors such as natural disasters and the pandemic, result in a variety of inventory problem.
Source: Supply Chain Game Changer, 2022
The COVID-19 pandemic impacted supply chains
Workers migrated.
Workers slowly migrated to better-paying industries, stayed home to collect stimulus checks or protect themselves from COVID-19, or fell sick from COVID-19. The resulting shortage of truck drivers and port workers made the movement of merchandise difficult in North America.
“… ships were waiting four weeks to unload due to the lack of workers on land.”
Shipping costs increased.
Sea transportation is an oligopoly. Only seven companies account for 77% of the global sea-transportation market. Sea transportation accounts for the movement of 90% of goods around the world. The impact of rising fuel costs, a lack of workers, and government-mandated pandemic control measures resulted in rising shipping costs.
“… the average global value of transporting a container went from $1,362 USD in November 2019, to $9,628 in February 2022 …”
China’s zero-COVID policy had global impacts.
China is the world’s largest exporter of goods and the largest trade partner of the North American economies. China’s zero-COVID policy was a crushing blow to global supply chain reliability.
“… average shipping times from China doubled …”
Consumer demand was volatile.
Stimulus checks to individuals and businesses sparked a quick recovery in demand. Many people had more money to spend and, by mid-2020, most businesses were rushing to revise their demand forecasts due to the explosive growth in e-commerce activity.
“… global e-commerce has jumped to $26.7 trillion, up by more than 4% ...”
Source of quotes: McGill Business Law, 2022
Supply chains were not prepared for a fast recovery. Rapid cratering of demand, followed by global supply and logistical challenges, resulted in businesses not being ready to address the pent-up demand as economies reopened.
Multiple factors impacted supply chains. Pandemic-related restrictions, sick workers, inflation, and geopolitical events, as well as the traditional lean principles that businesses operated by, contributed to supply chain disruptions.
Globalization is on the decline. The last 30 years of global economic activity led to the integration of economies. Globalization linked supply chains to create an extremely complex and interdependent network. Recent struggles are leading to the development of more localized supply chains.
Source: McGill Business Law, 2022
The vulnerability of just-in-time (JIT) inventory management was exposed
Pre-Pandemic
Geopolitical Events
The world has seen significant changes in global trade. Trade wars between the US and China and between the US and the EU, export restrictions by Japan on South Korea, and Brexit are a few examples of geopolitical events that impacted the cross-border movement of goods even before the pandemic hit.
Aggressive Just-in-Time/Lean Manufacturing
For decades, companies emulated Toyota’s production system by collaborating successfully with their suppliers to ensure the availability of raw materials and parts “just-in-time.” While efficient and effective when the supply of goods is moving freely, this methodology failed to account for disruptive events, such as the pandemic and trade wars.
Pandemic
Demand Volatility
Government-mandated restrictions broke supply lines, delayed shipments, and injected variability in the demand for products and services. This led to a mad rush for essential items such as toilet paper, disinfectant wipes, and food products. Empty shelves became common at many stores.
Stimulus Boost
Stimulus packages were introduced to provide relief funds to businesses and affected workers. Financial aid directly boosted spending on consumer products, which had seen a sharp decline in 2020.
Logistical Challenges
Disruption to global supply chains have trickled down to the logistics sector, which had to deal with labor shortages and high demand for goods from stimulus packages and rising use of e-commerce services.
Shortage of Skilled Labor
When businesses started reopening, they were faced with a shortage of labor. Sickness from COVID-19, restrictions on movement, and active unemployment benefits and stimulus checks resulted in businesses having a difficult time attracting and retaining workers.
Non-Pandemic
War in Eastern Europe
More than 600,000 global businesses rely on supply from Russia and Ukraine. The Russian invasion of Ukraine has directly impacted the prices of global commodities. This has resulted from a shortage of skilled labor due to workers from Russia and Ukraine being diverted to war efforts.
Product Recalls
Inventory of baby formula was impacted by a recall. Abbott Labs issued a voluntary recall of its baby-formula products manufactured in Michigan after a Food and Drug Administration (FDA) inspection found traces of a pathogen at Abbott’s factories and production had to be shut down. This affected the availability of formula for months.
Regulatory Challenges
Regulatory policies played an important role during the pandemic. While governments had to step in to prevent the hoarding of critical personal protective equipment (PPE) supplies and to procure imports of baby formula, inflexible regulation had a negative impact on the availability of generic medicines, such as Tylenol, in North America.
COVID-19 + JIT = shortage of consumer goods
Over the past three years, consumers have had to live with widespread global shortages of goods from pandemic-related shocks to supply chains and years of aggressive lean inventory policies enforced by companies across durable and non-durable sectors.
Product availability delays
"Due to industry-wide impacts of COVID-19 on the global supply chain, we are currently experiencing limited availability and significant delays for certain products in-store and online."
Source: IKEA, 2022
Production delays
"… ongoing supply chain issues have significantly impacted our ability to build intra-aortic balloon pumps (IABPs), intra-aortic balloon catheters (IABs) and spare parts due to raw material shortages."
Source: Getinge, 2022
Parts shortages
"The semiconductor shortage and the impact to production will get worse before it gets better. We have work to do to get our industry footprint back to firing on all cylinders."
Source: Ford, 2022
Impacts to pharmaceutical supply chains
The Drug Shortage Staff within the FDA’s Center for Drug Evaluation and Research (CDER) has asked manufacturers to evaluate "… any area of the supply chain that may be impacted due to the COVID-19 outbreak."
Source: FDA, 2022
Fluctuating demand
"As shortages spread across the country, we ramped up operations, and have been working around the clock to produce more formula and getting it to stores more quickly."
Source: Reckitt, 2022
Stock availability issues
"We know you may be having trouble finding our pediatric TYLENOL® products and we know it can be frustrating."
Source: Tylenol, 2022
Failure to manage inventory effectively resulted in a 5% to 7% annual decline in revenue for EU and North American companies, according to a report by The Economist Intelligence Unit
Source: Mechanical Power, 2022
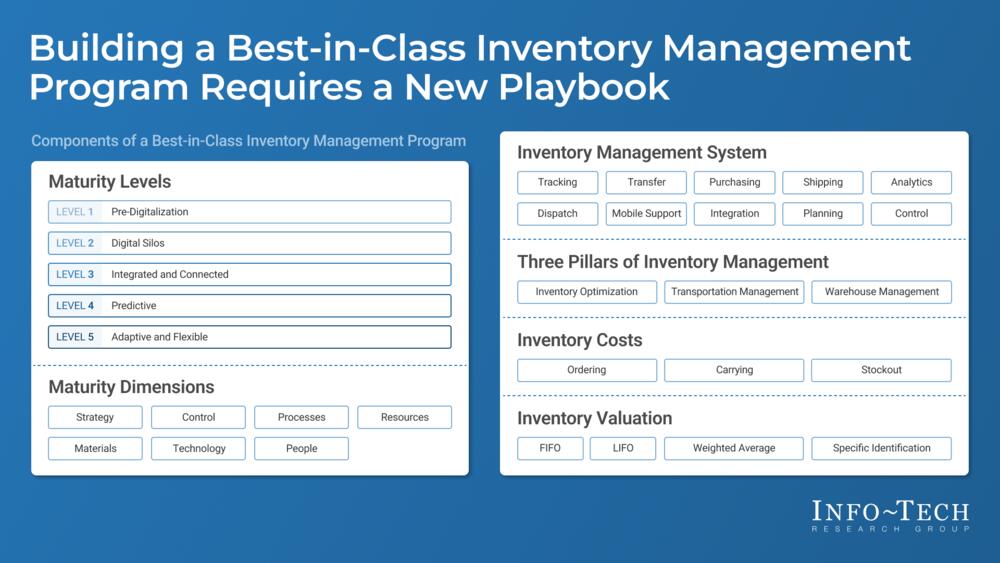
About Info-Tech
Info-Tech Research Group is the world’s fastest-growing information technology research and advisory company, proudly serving over 30,000 IT professionals.
We produce unbiased and highly relevant research to help CIOs and IT leaders make strategic, timely, and well-informed decisions. We partner closely with IT teams to provide everything they need, from actionable tools to analyst guidance, ensuring they deliver measurable results for their organizations.
What Is a Blueprint?
A blueprint is designed to be a roadmap, containing a methodology and the tools and templates you need to solve your IT problems.
Each blueprint can be accompanied by a Guided Implementation that provides you access to our world-class analysts to help you get through the project.
Talk to an Analyst
Our analyst calls are focused on helping our members use the research we produce, and our experts will guide you to successful project completion.
Book an Analyst Call on This Topic
You can start as early as tomorrow morning. Our analysts will explain the process during your first call.
Get Advice From a Subject Matter Expert
Each call will focus on explaining the material and helping you to plan your project, interpret and analyze the results of each project step, and set the direction for your next project step.
Unlock Sample ResearchAuthor
Shreyas Shukla
Contributors
- Brian Buddemeyer, Group Chief Information Officer, Spang & Company
- 2 anonymous company contributors
Unlock Advanced Inventory Management
Get Instant Access
Our systems detected an issue with your IP. If you think this is an error please submit your concerns via our contact form.
This content is exclusive to members.
Get instant access by signing up!
Our systems detected an issue with your IP. If you think this is an error please submit your concerns via our contact form.
Search Code: 101805
Last Revised: June 23, 2023
Book an Appointment
IT Research & Advisory Services
Our systems detected an issue with your IP. If you think this is an error please submit your concerns via our contact form.