Deliver Operational Efficiency Through Predictive Maintenance
Predictive maintenance is the answer to higher production throughput and lower maintenance costs.
Speak With A Representative
Request Content Access
Our systems detected an issue with your IP. If you think this is an error please submit your concerns via our contact form.
- Production is measured by throughput, which is a major component of on-time in-full, and downtime impairs OTIF.
- Reactive maintenance causes high costs for spare parts inventory.
- Reactive maintenance drives up the costs of secondary part failures, as failures are more catastrophic.
Our Advice
Critical Insight
- Sixty percent of companies are still doing reactive maintenance.
- The expected maintenance cost reduction due to predictive maintenance is between 25% and 35%.
- Reduction in downtime is up to 45%.
Impact and Result
- Predict: problems based on tolerance.
- Enable: proactive actions (predictive instead of reactive maintenance).
- See: prevention of downtime, increased productivity, and higher customer satisfaction.
Deliver Operational Efficiency Through Predictive Maintenance Research & Tools
1. Deliver Operational Efficiency Through Predictive Maintenance Storyboard – Learn about how predictive maintenance improves your production business at a lower maintenance cost.
Move from preventative and reactive maintenance to the higher quality, lower cost predictive maintenance methodology.
2. Deliver Operational Efficiency Through Predictive Maintenance Implementation Roadmap Tool – Ensure the right people are taking the correct actions at the correct time and the best solution is chosen.
Use this tool to map out your predictive maintenance implementation planning process.
Speak With A Representative
Request Content Access
Our systems detected an issue with your IP. If you think this is an error please submit your concerns via our contact form.
Deliver Operational Efficiency Through Predictive Maintenance
Predictive maintenance is the answer to higher production throughput and lower maintenance costs.
Analyst Perspective
Predictive maintenance is a must-have for continuous uptime and quality excellence.
The more established/historical maintenance management techniques cannot be replaced by predictive maintenance in all situations. However, predictive maintenance is a powerful addition to a thorough, all-encompassing strategic plant maintenance program.
Predictive maintenance programs involve scheduling specific maintenance operations as they are needed by plant equipment, as opposed to standard maintenance management programs, which rely on routine servicing of all machinery and quick response to unexpected failures.
The conventional run-to-failure and preventive programs must still be used in some capacity. However, in addition to offering a more dependable scheduling tool for typical preventive maintenance work, predictive maintenance can lower the incidence of unexpected failures.
Equipment manufacturers in all types of industries use the industrial internet of things (IIoT) for production and for achieving initial value. But when IIoT is used alongside predictive maintenance and service, organizations can make the most of their data to increase uptime, improve safety, and identify hazardous situations.
Info-Tech's approach focuses on an analyst's investigation of the challenges in the market and feedback on how you can leverage a predictive maintenance program to optimize your production environment.
Kevin Tucker
Principal Research Director, Manufacturing Research
Info-Tech Research Group
Executive Summary
Your Challenge | Common Obstacles | Info-Tech's Approach |
Your production operation lacks predictability, and the production team cannot see what is happening throughout the process. The CIO must work closely with operations leaders to identify ways to enable better technology support. You want to implement a program that avoids run-to-failure and the ripple effects of catastrophic outages. Your downtime is longer than necessary because service people are often unavailable when equipment or assets go down. |
Your organization is not capturing enough information for decision making or is capturing all the information manually. The business only knows reactive maintenance and does not have the skills or knowledge of other programs. Shop floor equipment or assets have not been connected by the internet of things (IoT). Equipment has proprietary sensors that are not easy to connect into a central data lake for planning purposes. |
Improve your maintenance plans by using our approach to understand the needs of your business and how predictive maintenance can help. Use our tools to evaluate your organization's current state of maturity, identify software tools to help, and assist with the implementation. Adopt a sensing-based approach that uses a holistically interconnected environment for end-to-end capture of information to improve usage lifecycle visibility. Work closely with our advisors, who can provide both strategic and tactical decision-making advisory services. |
Info-Tech Insight
Predictive maintenance is used in conjunction with IIoT and maintenance services so that organizations can make the most of their data to increase uptime, improve safety, reduce maintenance costs, and identify hazardous situations before they occur.
What is predictive maintenance?
Establishment of a decision-making approach to determine potential equipment failures
Predictive maintenance foresees issues before they arise by using historical and current data from numerous areas of your operation, such as sensors and built-in detectors that monitor tolerance levels.
Predictive maintenance uses data analysis tools and procedures to enable proactive management of the devices. It finds anomalies within your operation and potential flaws in your equipment and processes so you can correct them before they break. This is called the predictive maintenance (PdM) technique.
Predictive maintenance enables the maintenance frequency to be as low as feasible to prevent unscheduled reactive maintenance and to avoid incurring costs for excessive amounts of preventive maintenance.
Know the different maintenance methods
Each method has a distinct purpose and cost.
There is a cost associated with each method of maintenance being performed at an organization. The more important challenge is deciding on which method to be used and at which point in time. No single method is right for all situations.
Preventative
- Requires maintenance to be planned for set times, based on supplier guidelines
- Uses meters and software to track service times
- Provides asset health indications at the cost of downtime
- Requires planned downtime
- May run to failure if the timings are wrong
Predictive
- Is a proactive approach to servicing
- Combines the use of technology and early corrective action
- Uses asset sensing technology and software, along with data analytics
- Should not run to failure
- Requires less downtime and is less likely to have catastrophic failures
Reactive
- Requires fixing of problems as they arise
- Needs spares on hand for all potential situations
- Often requires extensive downtime
- May have a ripple effect because of running to failure, causing more parts to fail
- Requires skilled staff to be on hand 24/7 to perform immediate service
Involve your key stakeholders
Every business has different stakeholders and services.
1 Executive Management
The executive management team needs to be involved with determining which approach will be used for which equipment. In addition, the team will need to approve the up-front budget dollars necessary to run the predictive maintenance program.
2 Manufacturing Engineers
The manufacturing engineers are responsible for oversight of the equipment and the procedures for both setups and maintenance procedures. They will need to work with the suppliers to determine the tolerances used as boundaries to predict service needs.
3 Production Management
These stakeholders are vital for providing end-to-end communication and setting expectations. They will need to consider scheduling and customer impact implications as a result of any planned or unplanned downtime.
4 Maintenance Techs
The maintenance technicians have a difficult role to perform since they may be conducting maintenance across multiple work centers. They may also be working with external suppliers for maintenance and commissioning or decommissioning of equipment.
Choosing predictive maintenance
Do not underestimate the initial costs for setup/testing. Choose predictive maintenance based on your uptime priority need.
ADVANTAGES
- Maximizes equipment uptime
- Minimizes how often equipment needs to be maintained
- Minimizes the cost of parts and the inventory of spare parts on hand
- Increases operatory safety and production capacity
- Improves product design
- Reduces waste
DISADVANTAGES
- Can involve a higher upfront cost, especially during the learning stages
- Requires a new skill level to capture and interpret the data; these are high-end skills, which can be difficult to acquire
- Must be implemented strategically; not all assets are good choices for predictive maintenance
- Can require complicated initial setup
Predictive maintenance is taking off
COVID-19 was a big awakening for many businesses, when they could not get services during unplanned downtime.
Size of the predictive maintenance market worldwide in 2020 and 2021, with a forecast for 2022 to 2030 (in US$ billion)
Source: Statista, 2023
A long way to go to replace reactive maintenance
Too many companies are still doing costly reactive maintenance as their standard maintenance method.
Reactive
60%
Reactive maintenance is the most expensive way to conduct maintenance. However, a high percentage of companies are still doing it.
vs.
Predictive
75%
The good news is that a much higher percentage of companies are now prioritizing predictive maintenance as a key priority for their business.
Source: Finances Online, 2023
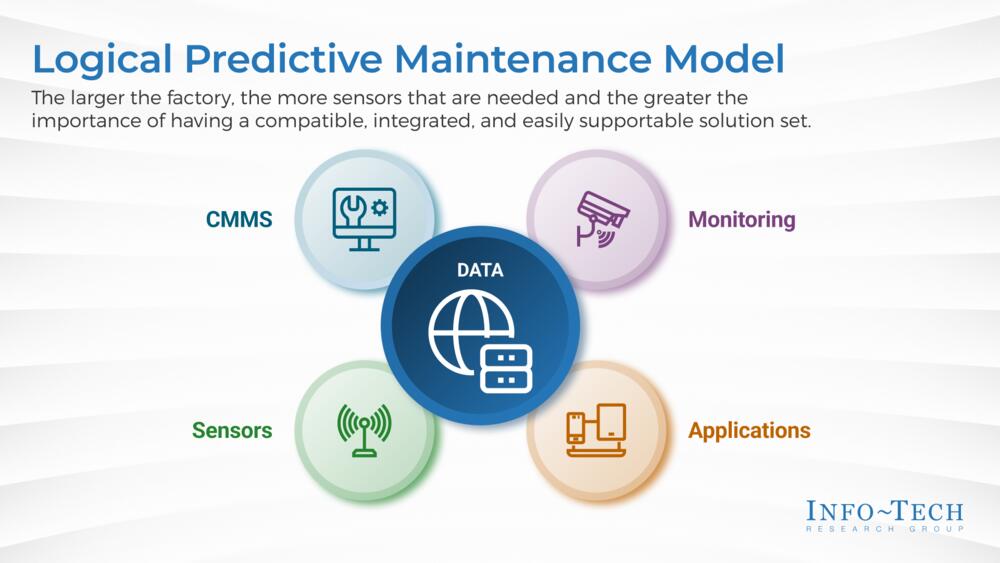
About Info-Tech
Info-Tech Research Group is the world’s fastest-growing information technology research and advisory company, proudly serving over 30,000 IT professionals.
We produce unbiased and highly relevant research to help CIOs and IT leaders make strategic, timely, and well-informed decisions. We partner closely with IT teams to provide everything they need, from actionable tools to analyst guidance, ensuring they deliver measurable results for their organizations.
What Is a Blueprint?
A blueprint is designed to be a roadmap, containing a methodology and the tools and templates you need to solve your IT problems.
Each blueprint can be accompanied by a Guided Implementation that provides you access to our world-class analysts to help you get through the project.
Talk to an Analyst
Our analyst calls are focused on helping our members use the research we produce, and our experts will guide you to successful project completion.
Book an Analyst Call on This Topic
You can start as early as tomorrow morning. Our analysts will explain the process during your first call.
Get Advice From a Subject Matter Expert
Each call will focus on explaining the material and helping you to plan your project, interpret and analyze the results of each project step, and set the direction for your next project step.
Unlock Sample ResearchAuthor
Kevin Tucker
Unlock Deliver Operational Efficiency Through Predictive Maintenance
Get Instant Access
Our systems detected an issue with your IP. If you think this is an error please submit your concerns via our contact form.
This content is exclusive to members.
Get instant access by signing up!
Our systems detected an issue with your IP. If you think this is an error please submit your concerns via our contact form.
Search Code: 102595
Last Revised: August 21, 2023
TAGS:
preventive maintenance, predictive maintenance, predictive maintenance software, predictive maintenance tools, predictive maintenance vs preventive maintenance, predictive maintenance technologies, predictive maintenance solutions, benefits of preventive maintenance, types of predictive maintenance, predictive maintenance analytics, predictive maintenance in manufacturing, predictive maintenance techniques, predictive maintenance challenges, predictive maintenance strategy, predictive maintenance equipment, benefits of predictive maintenance, predictive maintenance best practices, predictive maintenance productsBook an Appointment
IT Research & Advisory Services
Our systems detected an issue with your IP. If you think this is an error please submit your concerns via our contact form.