Digital Twins in Manufacturing
Empowering manufacturers by connecting the physical and the virtual.
While digital twins bring several benefits to manufacturers who implement them, there are significant barriers that make it a challenge to adopt this technology, including:
- Absence of interoperability and data compatibility.
- Lack of robust computational infrastructure and adequate network connectivity.
- Concerns related to protecting sensitive information, preventing unauthorized access, and ensuring compliance with data protection regulations.
- Absence of specialized skills, including data analytics, simulation modeling, and system integration.
- Resistance to change, lack of buy-in from stakeholders, and cultural barriers.
- Prohibitive cost and long return on investment periods.
Our Advice
Critical Insight
Embracing digital twins is not just a technological advancement but a paradigm shift that empowers manufacturers to reshape their operations, enhance competitiveness, and redefine industry standards.
Impact and Result
Embracing digital twin technology in the manufacturing industry offers a myriad of advantages, including:
- Enhanced Product Development: Digital twins enable rapid prototyping and virtual testing, reducing the time and costs associated with physical prototypes.
- Optimized Production Processes: Manufacturers can simulate different production scenarios to identify bottlenecks, optimize workflows, and improve overall efficiency.
- Predictive Maintenance: Digital twins facilitate predictive maintenance by analyzing real-time data, allowing businesses to address maintenance needs before equipment failure occurs.
- Reduced Downtime: With real-time monitoring and predictive capabilities, digital twins help minimize unplanned downtime, leading to increased productivity.
- Improved Quality and Safety: Manufacturers can ensure product quality and safety by identifying and rectifying issues in the virtual environment before they manifest in the physical world.
- Informed Decision Making: Data-driven insights from digital twins empower manufacturers to make well-informed decisions, driving continuous improvement.
- Remote Monitoring and Control: Digital twins enable remote monitoring and control of assets and processes, enabling efficient management across distributed locations.
Digital Twins in Manufacturing Research & Tools
1. Digital Twins in Manufacturing Deck – Research that provides a detailed overview of the applications of digital twins in manufacturing, exploring their potential to revolutionize the industry.
As factories become increasingly complex and interconnected, traditional approaches to production and maintenance are facing unprecedented challenges that demand innovative solutions. This research examines how digital twins can address critical challenges and unlock new opportunities.
2. The Ultimate Buyers Guide to Digital Twins in Manufacturing – A guide to help navigate this innovative technology landscape.
This comprehensive buyers guide will equip manufacturers with the knowledge and insights they need to make informed decisions. Whether just starting their digital twin journey or seeking to optimize an existing implementation, this guide will serve as their go-to resource.
3. Digital Twin Readiness Evaluation Tool for Manufacturing – A detailed description of considerations to be made before preparing to implement digital twins.
This tool will help manufacturers assess the maturity of their current state and compare it to their desired maturity state to judge their level of readiness for digital twin solutions. On completion, the tool provides specific recommendations to help them get to the right level of readiness for digital twin implementation.
Digital Twins in Manufacturing
Empowering manufacturers by connecting the physical and the virtual.
Analyst Perspective
Empowering manufacturers by connecting the physical and the virtual.
The manufacturing industry has undergone a profound transformation fueled by technological advancements and the rise of Industry 4.0. As factories become increasingly complex and interconnected, traditional approaches to production and maintenance are facing unprecedented challenges that demand innovative solutions. Factors such as rising costs, stringent quality requirements, intense global competition, and the need for increased operational efficiency have placed tremendous pressure on manufacturers worldwide. To meet these challenges head-on, the concept of digital twins has emerged as a game changer.
Digital twins serve as virtual replicas of physical assets, capturing real-time data and providing an accurate representation of their physical counterparts. By combining sensor data, machine learning algorithms, and advanced analytics, digital twins offer unparalleled insights into the performance, maintenance, and optimization of manufacturing processes. They enable manufacturers to monitor, simulate, and predict various scenarios, facilitating data-driven decision making and enhancing operational efficiency.
This research delves into the applications of digital twins in manufacturing, exploring their potential to revolutionize the industry by addressing critical challenges and unlocking new opportunities. From product design and prototyping to production planning, supply chain management, and predictive maintenance, digital twins offer a holistic approach to addressing the challenges faced by the industry. By analyzing real-world examples, we will explore how digital twins have revolutionized manufacturing practices, showcasing their capacity to streamline operations, enhance productivity, and drive innovation.
Shreyas Shukla
Principal Research Director, Manufacturing Industry
Info-Tech Research Group
Executive Summary
Your ChallengeYou are grappling with multiple challenges while trying to stay ahead of the curve on Industry 4.0 initiatives:
|
Common ObstaclesAbsence of interoperability and data compatibility. Lack of robust computational infrastructure and adequate network connectivity. Concerns related to protecting sensitive information, preventing unauthorized access, and ensuring compliance with data protection regulations. Absence of specialized skills, including data analytics, simulation modeling, and system integration. Resistance to change, lack of buy-in from stakeholders, and cultural barriers. Prohibitive cost and long return on investment periods. |
Info-Tech’s ApproachInfo-Tech Research Group recognizes that digital twins have significant benefits, including the capacity to streamline operations, enhance productivity, and drive innovation. Choosing the right technology will help accelerate progress on sustainability. Info-Tech will provide:
|
Embracing digital twins is not just a technological advancement, but a paradigm shift that empowers manufacturers to reshape their operations, enhance competitiveness, and redefine industry standards.
Unplanned downtime and preventative maintenance result in significant costs for manufacturers today
Inefficient maintenance is a big contributor to unplanned downtime. This is potentially one of the most disruptive, expensive events that can occur for a manufacturer, second only to a major safety or environmental mishap. A whopping 82% of companies have experienced at least one unplanned downtime within the last three years.
- The average manufacturer experiences 800 hours of equipment downtime per year – that’s more than 15 hours per week.
- Unplanned downtime costs industrial manufacturers up to $50 billion a year.
- Shutdowns can eat up to 1% to 10% of production time.
- A typical plant spends $100 million to $400 million a year on maintenances.
Source: Forbes, 2022
One minute of downtime costs:
- The Airline Industry: $65*
- Data Centers: $8,851
- The Automotive Industry: $22,000
*Technical problems caused delays for more than 1,800 flights in April 2023, costing Southwest Airlines $800 million. This day-long ordeal cost Southwest around $300 per flight per minute.
Source: Business Insider, CNBC
Obvious Costs
- Labor:
- Direct labor
- Overtime
- Outside contractors
- Production:
- Wastage
- Reduced capacity
- Testing and quality control
- Restart
- Finances:
- Lost revenues
- Tighter profit margins
Hidden Costs
- Overhead:
- Idled operators
- Indirect labor
- Parts
- Shipping
- Utilities
- Business:
- Lost sales
- Customer service risks
Manufacturers are beginning to see the value in implementing digital twin solutions.
- The digital twin market is expected to reach $35.8 billion by 2025
- It is expected to grow at a CAGR of 38.2% from 2020 to 2025.
- The manufacturing industry holds the largest market share in the digital twin market.
Source: Traction Technology
Digital twins are fast becoming a strategic priority for manufacturers
Digital twins provide significant benefits across the entire lifecycle of a manufactured product. Digital twins not only impact the bottom line but also contribute to revenue by improving both the efficiency and quality of how manufacturers execute on the shop floor.
Adoption
69% of manufacturers currently leverage digital twin technology.
- 97% of manufacturers think digital twin solutions are important to their organization.
- 71% of manufacturers have begun investing in digital twin technologies within the last year.
Intent
85% of manufacturers not using digital twin technology are planning to implement soon.
- 54% of remaining manufacturers have a digital twin initiative on their roadmap.
- 35% of remaining manufacturers intend to change their business model using digital twins.
Outcomes
92% of manufacturers feel digital twins have made their products and processes more sustainable.
- 62% of manufacturers are seeing reduced maintenance and warranty costs.
- 73% of manufacturers are seeing higher energy efficiency and less wastage from digital twin use.
Source: Altair Engineering, MSG Group
“Real benefits exist for companies that implement a digital twin … virtual costs diverge with physical costs increasing at the rate of inflation and virtual cost decreasing on an exponential basis … ” — Grieves & Vickers
Digital twins can address manufacturing challenges
Digital twins can help transform decision making while saving organizations significant amounts of time and money. Right from product design to testing, digital twins has an impact on prototyping, iterating, launching to market, and post-launch maintenance, covering the entire product lifecycle.
Challenges faced by manufacturing organizations:
Long Product Development and Time-to-Market Cycles
Development of physical products is a complex exercise. Conceptualization, design, prototyping, testing, and getting to start-of-production stage is a time and cost intensive process that can be impacted by errors in design.
Expensive Testing and Design Change Cycles
Product testing and making design changes for compliance is expensive. In most cases, errors with design are only identified while testing physical prototypes in real-world conditions. Incorporating findings from this exercise into design changes and retesting new prototypes is an expensive proposition.
Unnecessary Scheduled Maintenance
Traditional, scheduled maintenance activities are disruptive and expensive. Due to the complexity of modern machines with a large variety of components which each have their own maintenance requirements, traditional methods of managing this process using techniques like MTBF or doing scheduled maintenance are inaccurate and unnecessary.
Inaccurate Decisions
Real-world decision making is inaccurate because not enough testing or scenario analysis is done. These decisions are made on the basis of expert recommendations, without considering all possible scenarios for product, system, or process.
Source: Perforce
Digital twins can resolve challenges by enabling:
- Easier Prototyping – Through identification of errors early in the prototype process and across multiple design options.
- Faster Product Development – Digital designs, prototyping, testing, and even changes can be achieved faster.
- Reduced Time-to-Market – Since product development and testing is faster, products can launch earlier without impacting quality or safety.
- Better Testing – Through rapid identification of issues by replicating complex testing scenarios.
- Predictive Maintenance – Can reduce downtime by monitoring performance and predicting issues before they occur.
- Improved Decision Making – By incorporating real-time data from the physical world and running rapid simulations to test new concepts virtually.
“Digital-twin technologies can drive a revenue increase of up to 10%, accelerate time-to-market by as much as 50%, and improve product quality by up to 25%.”
— “Digital Twins: The Art of the Possible,” McKinsey & Company, 2022
Digital twins can reduce cost, improve productivity, and enhance innovation
Benefits
Real-Time Monitoring
Digital twins provide a real-time, in-depth view of a complex physical object or system.
Improved Business Outcomes
Digital twins enable businesses to make better decisions, translating into more enduring customer relationships and profitability.
Improved Collaboration
Planners, engineers, and technicians have 24/7 access to the same process and system information.
Improved Customer Satisfaction
Digital twins enable deeper insight into customer’s needs so businesses can deliver higher quality products.
Lower Maintenance Costs
Digital twins allow businesses to understand potential sources of failure so proactive actions can be taken to prevent disruption and downtime.
Improved Productivity
Digital twins reduce downtime and allow for system/process optimization, thus improving productivity.
Faster Production Times
Digital twins enable optimization of manufacturing processes, allowing for faster production times.
Rapid Testing
Digital twins enable simulation of scenarios, allowing insight into potential points of failure faster than on physical prototypes.
Source: “Digital Twins in 2023,” AI Multiple, 2023
Digital twin solutions are transforming engineering projects:
- 3 minutes or less to find actionable asset information
- 2 months to deploy across the full business unit with a cloud solution
- 10% increased staff productivity
- 30% or more reduction in unplanned downtime
Source: Aveva, 2022
Guiding you through your digital twin journey
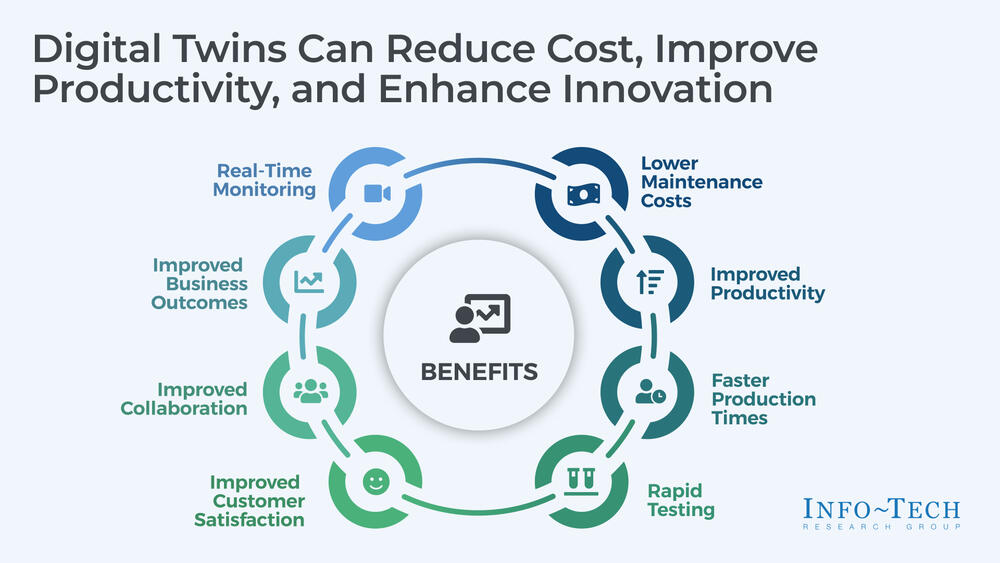
About Info-Tech
Info-Tech Research Group is the world’s fastest-growing information technology research and advisory company, proudly serving over 30,000 IT professionals.
We produce unbiased and highly relevant research to help CIOs and IT leaders make strategic, timely, and well-informed decisions. We partner closely with IT teams to provide everything they need, from actionable tools to analyst guidance, ensuring they deliver measurable results for their organizations.
What Is a Blueprint?
A blueprint is designed to be a roadmap, containing a methodology and the tools and templates you need to solve your IT problems.
Each blueprint can be accompanied by a Guided Implementation that provides you access to our world-class analysts to help you get through the project.
Talk to an Analyst
Our analyst calls are focused on helping our members use the research we produce, and our experts will guide you to successful project completion.
Book an Analyst Call on This Topic
You can start as early as tomorrow morning. Our analysts will explain the process during your first call.
Get Advice From a Subject Matter Expert
Each call will focus on explaining the material and helping you to plan your project, interpret and analyze the results of each project step, and set the direction for your next project step.
Unlock Sample ResearchAuthor
Shreyas Shukla
Contributors
- Karthik Bhat, Business Development Executive, Siemens AG
- Anish Arunachalam, Implementation Lead, Schneider Electric
- Eswara Prasad, Principal Architect, Cognizant Technology Solutions
- 1 anonymous contributor
Unlock Digital Twins in Manufacturing
Get Instant Access
Our systems detected an issue with your IP. If you think this is an error please submit your concerns via our contact form.
This content is exclusive to members.
Get instant access by signing up!
Our systems detected an issue with your IP. If you think this is an error please submit your concerns via our contact form.
Search Code: 103026
Last Revised: October 31, 2023
TAGS:
digital twin, manufacturing, Industry 4.0, smart manufacturing, IoT, IIoT, predictive maintenance, process optimization, product design, simulation, real-time, sensors, connected, virtual, efficiency, productivity, downtime, automation, autonomy, artificial intelligence, generative AI, visualization, factory, monitoringBook an Appointment
IT Research & Advisory Services
Our systems detected an issue with your IP. If you think this is an error please submit your concerns via our contact form.
Speak With A Representative
Request Content Access
Our systems detected an issue with your IP. If you think this is an error please submit your concerns via our contact form.