Factory of the Future – Smart Factory Trends for Durable Goods
An industry strategic foresight trends report
Speak With A Representative
Request Content Access
Our systems detected an issue with your IP. If you think this is an error please submit your concerns via our contact form.
- Embed
- Link
Share
×Speed
×Subtitles
×- Your operation is overly cautious, with a low appetite for transformational disruption in the operations.
- You are risking being left behind as the rest of the industry progresses in this digital and ESG conscious era.
- Your operation has difficulty attracting new customer segments and struggles to offer a compelling product in the competitive durable goods manufacturing space.
- Niche players have made your operation more vigilant; therefore, your objective is to modernize the factory quickly so that customers' satisfaction ratings from site audits will be positive.
- The effects of the pandemic are still apparent within your operation, most notably dealing with a shortage of labor, acquiring skilled labor, and supply chain disruptions.
Our Advice
Critical Insight
Transform your durable goods manufacturing business into a Smart Factory by analyzing the four driving trends that embrace the elements that create a real-time, data-driven decision-making factory that can adapt to shifting market conditions and thereby future-proof the manufacturing operation.
Impact and Result
- Identify: As a methodology, strategic foresight flows from the identification of signals to clustering the signals together to form trends, and uncovering what is driving the trends to determine which strategic initiatives are most likely to lead to success on an industry level.
- Prioritize: Further customize the scores to your manufacturing by tailoring the generalized weightings on an organization-specific level and determining the relevancy and timing to your operations. By doing so, your manufacturing can determine which trend and technology to prioritize for your Smart Factory initiative.
- Align: After establishing what trend and technology to prioritize, establish its benefits that closely align and promote the success of your business’ goals.
Factory of the Future – Smart Factory Trends for Durable Goods Research & Tools
1. Factory of the Future – Smart Factory Trends for Durable Goods Storyboard – This strategic foresight trends report highlights the technologies that are currently trending in the Durable Goods Smart Factory Manufacturing industry.
Learn about the four key trends that will help transform your durable goods manufacturing business technology initiative into a Smart Factory strategy.
Speak With A Representative
Request Content Access
Our systems detected an issue with your IP. If you think this is an error please submit your concerns via our contact form.
Member Testimonials
After each Info-Tech experience, we ask our members to quantify the real-time savings, monetary impact, and project improvements our research helped them achieve. See our top member experiences for this blueprint and what our clients have to say.
9.0/10
Overall Impact
5
Average Days Saved
Client
Experience
Impact
$ Saved
Days Saved
Testimonial
Anchor Packaging LLC
Guided Implementation
9/10
N/A
5
Shreyas is very knowledgeable and provides great insights. He understands the needs and tailor the answers to fit the needs of the organization. I ... Read More
Shreyas is very knowledgeable and provides great insights. He understands the needs and tailor the answers to fit the needs of the organization. I will continue to engage with him in this journey. Read Less
Factory of the Future – Smart Factory Trends for Durable Goods
An Industry Strategic Foresight Trends Report
Become a Smart Factory Analyst Perspective
The post-pandemic manufacturing environment is changing rapidly as companies have realized that employer and customer centricity are vital for success
By leveraging technologies to become a Smart Factory, companies can rapidly capture ROI and increase satisfaction.
Employees become super-skilled members of a cobotic world (human and robotic) where automatic visual recognition, self-healing, autonomous robots and robotic process automation are commonplace.
The new Smart Factory is a holistically connected environment that provides instantaneous and rich decision-making data. Employee and customer demands have changed, and technology is paramount for future success.
Developing a Smart Factory is the key to leadership in the market and defending against the market disruptors.
Every process will be improved across the people, process and technology used in the factory.
Sources:
Licari and Swanson, 2011. electronicsnotes, 2022.
metrology.news, 2019..Harring, 2021.
Smart technology can help companies because it is not a one-size-fits-all solution and can be modified to help individual businesses meet their specific needs.
Bill Berutti, CEO of Plex Systems (Harring, 2021)
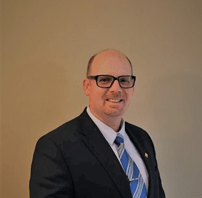
Kevin Tucker
Principal Research Director
Manufacturing, Supply Chain & Logistics.
Info-Tech Research Group
Smart Factory:
Success requires a flexible staffing model
The effects of the COVID-19 pandemic are still apparent, with manufacturing dealing with several key challenges:
- Labor – Retaining skilled labor, attracting replacement staff and uplifting skillsets for running existing, or implementing new technologies, has become highly problematic.
- Materials – Supply chain disruptions are a global problem that has disrupted the flow of goods, increased shipping costs, and elevated commodity prices, forcing some companies to stop operating.
- Part and Process Complexity – The more complex the part, the more expensive the labor costs for those that are unable to leverage technology for automation or cannot get the skilled staff to oversee the operations.
- Tooling, Fixtures and QA – Purchasing and building tooling has become more costly, while quality tools are more sophisticated (needing highly skilled technicians) and requiring more upfront cost for installation and setups.
- Customer/Staff Expectation Changes – Higher customer- and employee-centricity, where consistent information and services are expected across all channels.
- Accuracy and Precision – Accurate setup for good parts and precision of batches require data and analytics for monitoring and self-healing.
- Data and Connectivity – Security, proprietary equipment, and fragmented standards are all obstacles the smart factory must overcome.
Sources: Williams, 2022. U.S. BUREAU OF LABOR STATISTICS, 2020. Columbus, 2019.
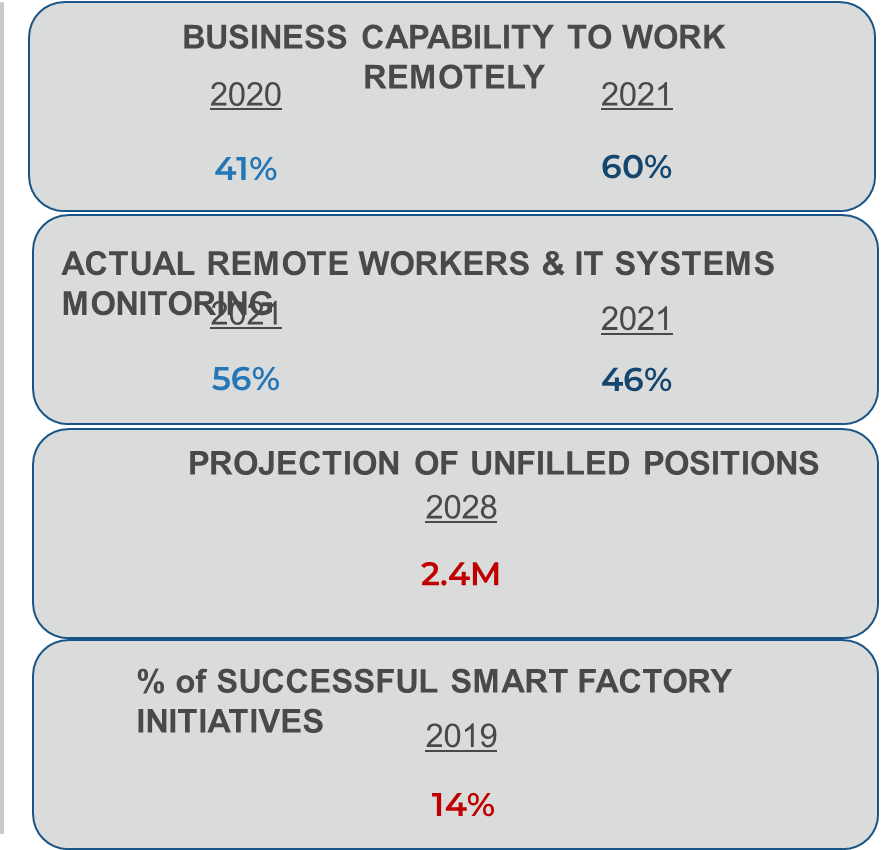
Smart Factory:
Get to Level 5 for Smart Factory Success
LEVEL 1 | Primarily Manual |
The Business utilizes paper-based and manual business processes. |
---|---|---|
LEVEL 2 | Partially Automated |
Some automation and data capture has been implemented. |
LEVEL 3 | Automated |
Data captured at every application and almost no manual processes. |
LEVEL 4 | Automated & Connected |
Automated and connected into a data lake for live data-driven decision-making capabilities. |
LEVEL 5 | Smart Factory |
Fully automated and connected with AI, RPA and ML for machine-intelligent decisions and self-healing. |
LEVEL 6 | Smart City Smart Economy |
Smart Factory:
Level 5 and Beyond
The Smart Factory opens a host of opportunities for Intelligent business:
Companies that have made the journey to the Smart Factory have reached into the center of the earth's core.
Why do we say this? For a manufacturing business, the core of the business is the production operation. It determines when, how much, and at what cost your products can be produced.
If the business achieves Level 5 Smart Factory capability, there suddenly becomes a wide range of services available for the company to track, trace and measure.
Smart Factory
Smart Mobile
Smart Grids
Smart Networks
Smart Services
Smart Vehicles
Smart Meters
Smart Buildings
Smart Cities
Smart Logistics
Smart Platforms
Smart Factory:
The CIO must consider new demands.
Change now or be left behind by the Competition.
Benefits of creating a Smart Factory:
- S Self-Optimizing Production Operations
- M Maintained by Predictive Intelligence Processes
- A Artificial and Augmented Intelligent Interactions
- R Realtime Data and Waste Reduction
- T Technology-based Live Digital Network
Sources: Bossard, 2022. Deloitte, 2022. Capgemini, 2019.
Smart Self-Optimizing Factory
- Mobility
- Global Talent
- Cloud & Sensing
- Predictive Intelligence
- Rapid & Reliable Supply
- Clean
- Cobotic Labor
- AI / ML Intelligence
Who’s investing in Smart Factory?
70% |
Manufacturers are undergoing Smart Factory Initiatives. |
---|---|
30% |
Transformed into Smart Factory operations in the past two years. |
41% |
Plan to be converted into Smart Factories within the next four years. |
Smart Factory:
Think end-to-end to become a Smart Factory
The tools, the skills and the processes are all vital considerations toward building new capabilities
Making Smart a Core Capability
- Realtime Tracking and Monitoring
- Inputs
- Outputs
- Contents
- Environmental Impact
- Automated calibration and tolerance tracking
- Self-configuring robotics
- Augmented Intelligence tied into the private cloud
- Digital twinning of the planning, simulation and design processes
- Tracking of assets and movements of both people and autonomous vehicles
“Connectivity requirements in a factory are very dependent on the use case and
application, and so the network also needs to support service differentiation.”
Sebastian Elmgren,
Portfolio Manager Smart Manufacturing,
Advanced Industries, Ericsson
By connecting our high-precision screwdrivers, we will see a 50% return on investment in year one. And, breakeven is reached in less than 2 years,
Tomas Qvist, President,
Nanjing Ericsson Panda Communication
(GSMA, 2018)
Smart Factory:
Making Labor a Priority
Having the correctly skilled labor to do the job
The competition for skilled labor has never been higher
Becoming a Smart Factory can reduce the labor burden by reducing the number of lower skilled labor levels and increasing the super-skilled labor levels of the company.
The labor market continues to be strained by "the great resignation" and the fact that the workforce shortages are expected to continue. There are some decisive actions that companies can take to combat the talent shortages:
Develop a continuous learning model.
Enable Smart Factory automation.
Hire and train a more diverse workforce.
Partner with local communities for recruitment.
Broaden the network to become more globally engaged for talent.
Become more creative at enabling virtual job options.
Sources: PrNewsWire, 2021. Nam.Org,2020. VettaFi, 2021. Food Logistics, 2021.
US Manufacturing Skills Gap Could Leave As Many As 2.1 Million Jobs Unfilled By 2030
Deloitte and
The Manufacturing Institute.
May 2021
Finding the right talent is 36% more challenging than it was back in 2018 even though more employees are looking for jobs.
CISION
May 2021
Smart Factory:
Labor challenges persist in European factories
The Labor concerns are less evident than the US, but still a factor
"The US relied on unemployment insurance and having people leave their original job during COVID, so there was perhaps much more turnover”
“ … Whereas in countries like Germany during COVID, people stayed in their job and the government subsidized the payroll of employers. So, in the US, you might have seen much more turnover and much more reorganization experimentation — which might explain why quits are now high in the US.“
Benjamin Schoefer,
UC Berkeley, Feb 2022
"The European Union is seeing its economic emergence from the unprecedented COVID-19 slowdown hampered by coronavirus-induced staff shortages, supply bottlenecks, runaway energy prices and subsequent inflation surges.”
Associated Press,
Feb 2022
Sources: Horowitz, 2021. Colijn and Brzeski, 2021. Kaplan, 2022. Axioglou and Wozniak, 2022.
Smart Factory:
The US has been hit hard by labor challenges
"Given the foundational role the manufacturing sector plays in our nation's economy, it is deeply concerning that at a time when jobs are in such high demand nationwide, the number of vacant entry-level manufacturing positions continues to grow. Attracting and retaining diverse talent presents both a challenge and solution to bridging the talent gap. To attract a new generation of workers, the industry should work together to change the perception of work in manufacturing and expand and diversify its talent pipeline."
Paul Wellener,
Vice Chairman and U.S. industrial products and construction leader, Deloitte LLP
"Manufacturers are proud to lead efforts to build stronger, more diverse and inclusive workplaces because we are committed to being the solution. These findings confirm the urgency of our mission and that we need not only to continue our work but to accelerate it. As we expand our programs at The Manufacturing Institute, and work with the National Association of Manufacturers on initiatives like our Creators Wanted campaign and tour, we're making sure that Americans of all backgrounds in all states can find a home in manufacturing and get equipped with the skills to seize these opportunities. With so many open jobs in manufacturing, we are uniquely positioned to welcome emerging and displaced workers into rewarding and meaningful careers."
Carolyn Lee,
Executive Director, The Manufacturing Institute
Source: Deloitte (prnewswire), 2021.
Smart Factory:
Market leaders are accelerating Smart Factory growth
Now is the time for smart technology adoption
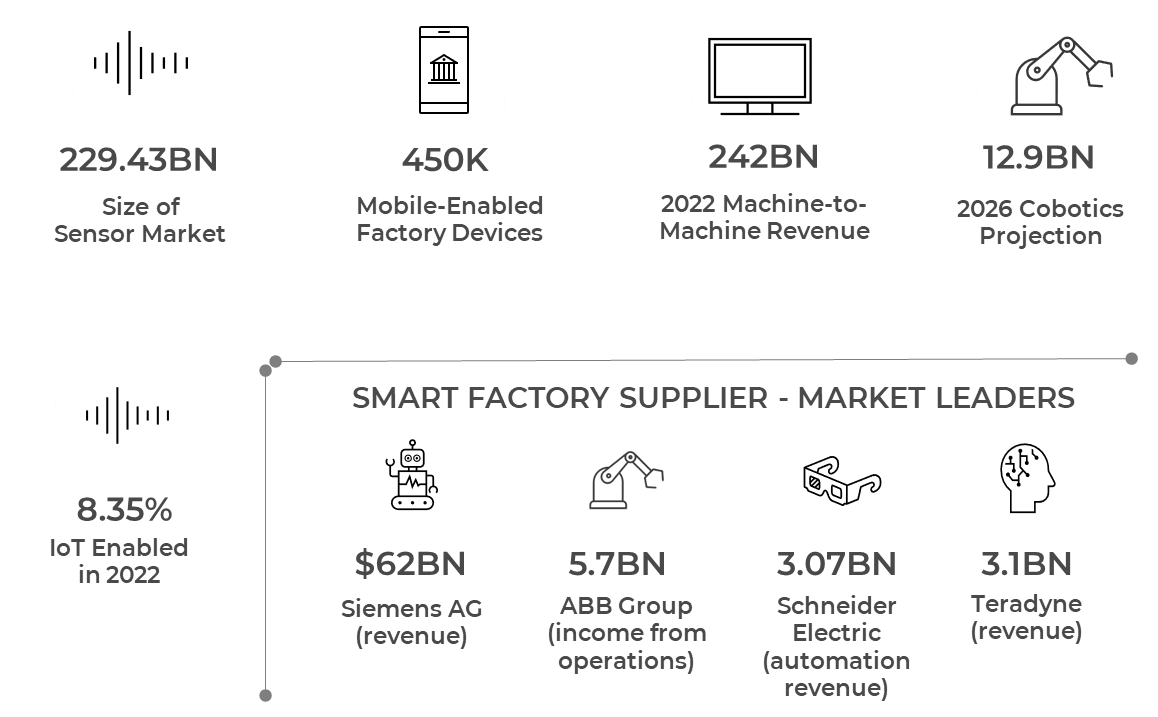
Smart Factory:
MATURE THE IT BUSINESS
FROM FIRE FIGHTER TO TRUSTED OPERATOR
According to our Durable Goods Manufacturing’s 2021 Benchmarking report, strategy is lagging behind other segments, and a lot of focus is still centered around large legacy applications. This problem is magnified by the onset of staffing and retention issues, which are difficult to resolve for Smart Factories. IT can only maintain relevance if it becomes a trusted operator. By leveraging new technology such as Industry 4.0, the IT organization must shift its weight to heavily focus on strategy and applications. The biggest challenge for IT is to get the skilled staffing for the move to the new ecosystem; however, those that achieve it will establish credibility with business stakeholders as transformational innovators.
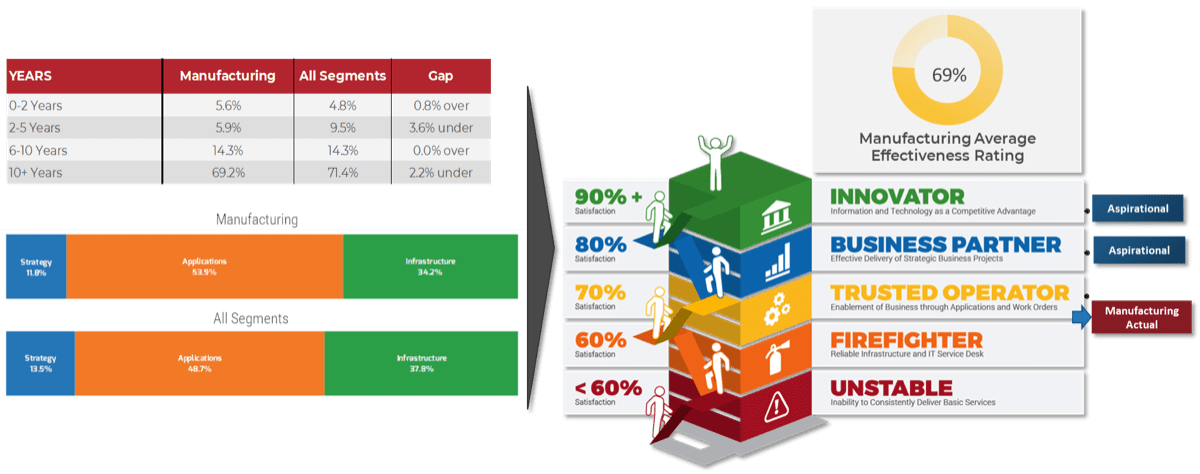
Smart Factory:
Obstacles to a Smart Factory technology initiative:
Prioritization
“I would say the lack of skilled resources is one of the biggest pain points that we encounter.”
Chander Damodaran,
Chief Architect, Digital at Brillio Consulting,
referring to IoT projects at large (IOT World Today)
On one hand there is a compelling case for developing a Smart Factory environment and thereby reducing the requirement for human labor. On the other hand, companies don’t want to endure upfront costs, and they fear employee losses.
- IoT has become central to the success of factories, as COVID-19 forced them to operate with new and essential automated methods.
- The proprietary nature of many manufacturing technologies has slowed progress due to the high cost of integration.
- Budgets are strained and high-level skills are difficult to find and keep.
Moving to Smart Factory is a challenge for many that are lagging behind the market. However, if they don’t elevate their capabilities, they will very likely become disrupted from the market.
Sources: Intech Open and The World Bank, 2019.
Break through the old mindset of thinking that doing more with less is sustainable.
In the modern era you will be left behind.
“As we look across the industrial sector, people are trying to run factories and supply chains with ever-leaner levels of staffing,”
Grant Erickson,
President of Thread Group.
Smart Factory:
The obstacles of a Smart Factory initiative: Persuasion
“ ‘If-it-ain’t-broke-don’t-fix-it’ idiom.
Smaller industrial companies find it very hard to justify replacements when the existing machine works perfectly.”
James Blackman,
Enterprise IoT Insights
In the United States alone, 86 percent of manufacturers believe that smart factories will be the main driver of competition by 2025.
Deloitte, 2020
Sources: Blackman, 2018. Phuyal, Bista and Bista, 2020.
Deloitte, 2022. Deloitte, 2020.
“Rising confidence in the industrial sector’s appetite for enterprise IoT solutions, including those based on emerging wireless technologies, encouraged Ericsson in June to double its forecast for low-power wide-area (LPWA) cellular connections to 3.5 billion by 2023.”
James Blackman, Enterprise IoT Insights
Evolving into a Smart Factory environment isn’t without its detractors and complications from interoperability, connectivity, financing, skills, fragmentation, safety, language, ROI, and security integration.
- The key benefit of Smart Factory or Intelligent Manufacturing is the holistic connectivity of the factory and the ability for staff to make real-time data-driven decisions.
- By implementing IoT and capturing data into a central processing system (hub), the organization can leverage the data to optimize all business processes.
- Although there is a lack of standards; companies that achieve Smart Factory capability open the doors to live tracking, live feeds, and market data beyond the factory.
Cloud computing and the Edge have opened endless possibilities for sharing, monetizing and making real-time decisions with data that offers opportunities for rapid and sustainable ROI.
Smart Factory:
Transforming from Manual to Smart
Smart Factory uses automation to streamline and increase profitability:
Manual Processes that need to be replaced:
- Printed work orders and paperwork.
- White boards.
- Manual loading, setting up, and unloading of parts.
- Manual operation of quality tools, jigs, and fixtures.
- Supervisors with clip boards walking around the factory.
- Manual recording of products and quantities.
- Lifting and moving of products by pump trucks and manual carts.
- Manual start and stop of the lines by operators.
- Finding problems after the work center has completed its processes.
- Manual tracking and recording of stage gates.
- Reports produced from data captured and entered after the fabrication process is completed.
- Use of larger aisles and racks enabling more room for people to work.
Exemplar Smart solutions that transform the Factory:
- All workorders, schedules, and whiteboards are automated.
- Electric forklifts and autonomous machines move, pack, wrap, transport, put-away, and pack the products.
- Cobotic setups, self-stopping, self-healing systems for product production.
- Computer-based validation systems.
- Holistically live connect with IoT and IIoT.
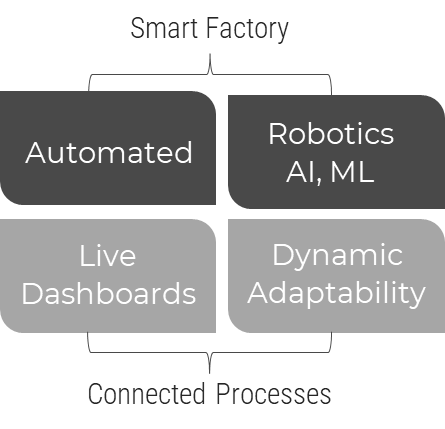
Smart Factory:
Business Perspective
As manufacturers embark upon the path to Smart Factory, they must consider how the new technological innovations will impact their staff and customers.
Benefits for Management
- Higher data quality.
- Improved product quality.
- Greater customer satisfaction.
- Everything becomes measurable.
- Lower total cost of ownership.
Potential Staff Takeaways
- Process simplification.
- Removal of error prone processes.
- Higher employee confidence, skills, engagement, and eventually satisfaction.
Potential Customer Takeaways
- Seamless customer experience through electronic omnichannel.
- Expanded value for (B2B) and (B2C) customers through real-time status.
- Meeting and exceeding expectations of the customer value chain.
- Enhanced levels of trust through all business interactions.
- Quote and pricing accuracy.
Smart Factory:
Build IT Integration for Connectivity and Value
- Interconnectivity is the secret sauce that enables the factory to transform itself from an operational factory to a high-performance Smart Factory.
- Integration enables the business to leverage current solutions such as AI, IIoT, and Big Data, and it lays the foundation for adoption of emerging technologies such as the metaverse.
- The Durable Goods Manufacturing Industry’s benchmarking data illustrates the lack of focus on strategy that is vital for businesses to become a Smart Factory.
- The move up the maturity ladder requires planning, executive buy-in, and budget support.
- Application focus must be toward new applications vs legacy applications that cannot leverage modern solutions such as Cloud and black box IIoT.
“Change is no longer optional:
If you don't keep up with the times the world will leave you behind and your outdated skills will cause the market to abandon your products and company.“
Kevin Tucker,
Principal Research Director, ITRG
Leverage Info-Tech Integration Resources
Build an Application Integration Strategy
Build a Data Integration Strategy
Build an Effective Enterprise Integration on the Back of Business Process
Smart Factory:
Foundational IT Elements
What does the business need from IT for the Smart Factory digital transformation to succeed?
Capturing live data combined with artificial intelligence for live data-driven decisions across the factory:
Sources: Herold, 2017.
Smart Factory:
Four enabling trends that will drive your success
Elastic Talent Platform
It’s no longer enough to have and retain talent. Transitioning and sustaining a Smart Factory environment must include a sophisticated talent strategy.
Cybernated Supply Chain
Whether operating domestically or locally, manufacturers must implement tools and partnerships with global supply chain partners and use demand planning to meet on-time-in-full (OTIF) KPIs.
Predictive Reality
Downtime is extremely expensive. If manufacturers’ production systems are down and cannot be serviced remotely, the cost escalates dramatically. Move from reactive to proactive self-correcting.
Contextual Intelligence
Artificial Intelligence, machine learning, autonomous robotics, and energy management systems will become the new normal. All processes will be adapting live.
Smart Factory:
Technologies that enable the Trends
The Smart Factory leverages the Industry 4.0 product set to create holistic automation, connectivity, and collaboration
TECHNOLOGY MAP | |||||
---|---|---|---|---|---|
CORE PRODUCTS | |||||
ROBOTICS |
IoT, IIoT |
AI, ML, NLP |
DATA ANALYTICS & DEMAND PLANNING |
CLOUD |
CYBERSECURITY |
|
|||||
ELEVATION PRODUCTS |
|||||
DIGITAL TWINNING |
BLOCKCHAIN |
DRONE & AUTONOMY |
3D ADDITIVE PRINTING |
AR, VR & METAVERSE |
COMPUTER/ROBOTIC VALIDATION |
|
Sources: McLaughlin, 2022. Herold, 2017.
Email Infographic
About Info-Tech
Info-Tech Research Group is the world’s fastest-growing information technology research and advisory company, proudly serving over 30,000 IT professionals.
We produce unbiased and highly relevant research to help CIOs and IT leaders make strategic, timely, and well-informed decisions. We partner closely with IT teams to provide everything they need, from actionable tools to analyst guidance, ensuring they deliver measurable results for their organizations.
MEMBER RATING
9.0/10
Overall Impact
5
Average Days Saved
After each Info-Tech experience, we ask our members to quantify the real-time savings, monetary impact, and project improvements our research helped them achieve.
What Is a Blueprint?
A blueprint is designed to be a roadmap, containing a methodology and the tools and templates you need to solve your IT problems.
Each blueprint can be accompanied by a Guided Implementation that provides you access to our world-class analysts to help you get through the project.
- Embed
- Link
Share
×Speed
×Subtitles
×Need Extra Help?
Speak With An Analyst
Authors
Kevin Tucker
Larry Fretz
Contributors
- Buddemeyer, Brian; VP, Information Technology Spang & Company
- Iseli, Stefan; Director IT Smart Factory, Comet AG
- Pretorius, Linda; Director IT & Business Transformation, MHI Canada Aerospace Inc.
- Schild, Andreas; IT Business Partner PCT, Comet AG
- Smith, Mike; CIO, Sonepar
- Stanley, Jay; VP IT, Heartland Food Products Group
- Teodorescu, Alexandru; Account Executive, PDSVISION
- Monthly Industry Roundtable Participant Feedback
Unlock Factory of the Future – Smart Factory Trends for Durable Goods
Get Instant Access
Our systems detected an issue with your IP. If you think this is an error please submit your concerns via our contact form.
This content is exclusive to members.
Get instant access by signing up!
Our systems detected an issue with your IP. If you think this is an error please submit your concerns via our contact form.
Search Code: 99563
Last Revised: September 27, 2022
TAGS:
manufacturing, Operations, Industry 4.0, Energy, IoT, IIoT, Ecosystem, Factory, Smart, employee, staff, scan, scanning, contactless, skills, operations trends, production, employee experience, retention, hiring, succession, customer value, production operation, integrated durable goods manufacturing reference architecture, manufacturing business growth, manufacturing operational excellence, manufacturing customer value, omnichannel, mobile, responsive design, DevOps, encryption, mobile engagement, telematics, GPS, supply chain, digital, automation, workshop, cybersecurity, collaboration, IT/OT, convergence, improvement, innovation, benchmark, capacity, staffing, cost reduction, cloud, predictive, business intelligence, hub, maintenance, strategy, strategic, cobotics, autonomous, robotics, AI, ML, NLP, AI/ML/NLP, intelligent, performance, comparison, vendors, suppliers, prototyping, digital twinning, 3D printing, Additive Manufacturing, Internet of Things, equipment, infrastructure, hyperlocal, microfactory, customer satisfaction, evaluation, initiatives, BMW, L'Oreal, functionality, agile, report, progress, on-shoring, diversified, Digital Twins, Demand Driven Planning, real-time, data-driven, big data, artificial intelligence, channel integration, data lake, computer based training, augmented reality, virtual reality, MES, TMS, WMS, MRP, DDMRP, Data Analytics, safety stock, buffers, Disruption, Green Manufacturing, ESG, circular, predictive intelligence, Industry NEXT, accuracy, zero downtime, decision-making, micro-internships, contextual, artificial, Cobotic, disruptors, Visual Recognition, fixtures, tools, kitting, fabrication, welding, shipping, monitoring, Cybernated, Elastic, logistics, self-optimize, self-healing, sensing, mobility, private, tolerance, Deloitte, Drone, AR, VR, Service, Inventory, Dispatch, Alumina, AdobeBook an Appointment
IT Research & Advisory Services
Our systems detected an issue with your IP. If you think this is an error please submit your concerns via our contact form.